МК в Саратове
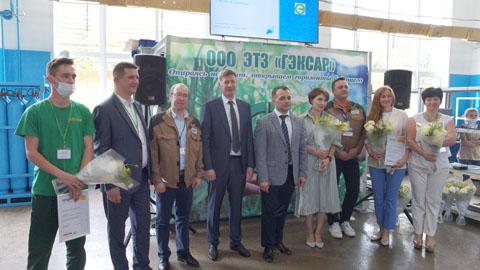
Рашид Бикташев: «Это только начало!»
Серьёзная экономия и оптимизация производства — вот основные результаты реализации нацпроекта на электротехническом заводе «ГЭКСАР»
На минувшей неделе электротехнический завод «ГЭКСАР» принимал высоких гостей. Для подведения первых итогов внедрения на предприятии технологий бережливого производства собрались министр экономического развития Саратовской области Андрей Разборов, руководитель проектов Федерального центра компетенций Юрий Васильев, руководство завода, сотрудники предприятия.
Всего полгода назад
Напомним суть вопроса. В число участников федерального национального проекта по повышению производительности труда и поддержки занятости электротехнический завод «ГЭКСАР» вошёл в конце такого сложного для всей экономики страны 2020 года. Цели проекта, как известно, измеряются в государственном масштабе: обеспечение к 2024 году темпов роста производительности труда средних и крупных предприятий базовых несырьевых отраслей экономики не ниже 5% в год. Прирост производительности труда к этому времени должен составить не менее 20%.
Думаем, не стоит и говорить, насколько важен проект для нашей страны. Достаточно такого факта: контроль за его реализацией осуществляется на самом высоком федеральном уровне. Курируют проект председатель правительства Российской Федерации Михаил Мишустин, первый заместитель председателя правительства РФ Андрей Белоусов, министр экономического развития РФ Максим Решетников.
Уже тогда, в самом начале, полгода назад генеральный директор ООО ЭТЗ «ГЭКСАР» Рашид Бикташев возлагал большие надежды на результаты реализации данного проекта, особо отмечая эффект оптимизации производства в условиях острой нехватки квалифицированных кадров:
— Все мы прекрасно понимаем: каким бы современным и высокотехнологичным ни было оборудование, без специалистов оно будет загружено от силы процентов на 30.
Важным моментом реализации проекта является и серьёзная поддержка, которую получает его участник. Так, со стороны Федерального центра компетенций осуществляется адресная поддержка предприятия, министерство труда курирует сферу занятости, и, наконец, министерство экономического развития отвечает за системные меры.
Приняв участие в национальном проекте, ООО ЭТЗ «ГЭКСАР» получило адресную поддержку, которая представляет собой квалифицированную помощь экспертов по устранению неэффективности производственного процесса непосредственно на предприятиях — участниках национального проекта, обучение сотрудников методам повышения производительности труда с использованием инструментов бережливого производства.
К последним относится, в частности, так называемая система «Пять С» — или «5S» — разработанная в Японии система организации и рационализации рабочих мест, направленная на повышение эффективности и управляемости операционной зоны, увеличение производительности труда, экономию времени и совершенствование корпоративной культуры. Концепция бережливого производства 5S подразумевает, что все сотрудники предприятия — от уборщицы до топ-менеджеров — соблюдают несколько простых правил. К слову, плакаты с ключевыми моментами данной системы до сих пор расположены в одном из цехов предприятия, как незыблемые правила, установленные теперь раз и навсегда.
Немаловажным является и определение семи видов потерь на производстве. Таких, например, как перепроизводство, бороться с которым рекомендуется работой по времени такта и текущей системе поставок; накоплению излишних запасов рекомендуется противопоставить вытягивающую систему производства, сокращение размера партий и сокращение времени на переналадку. Ненужной транспортировки удастся избежать в том случае, если на предприятии будет составлена карта потока создания ценности и оптимизация расположения оборудования и складских помещений. Вместо лишних движений — стандартизированная работа, повышение квалификации работников и порядок на рабочем месте. Время ожидания сократит оптимизация расположения оборудования, всеобщее обслуживание оборудования, тянущая система и производственные ячейки. Избыточной обработки можно избежать при условии организации стандартизированной работы и изучения потребностей клиента. Работать без брака поможет соблюдение правил трёх «не»: не принимай, не создавай, не переделывай брак, а также введение «ворот качества».
В итоге — совершенно потрясающие результаты: внедрение системы «Пять С» приводит к уменьшению несчастных случаев на производстве, улучшению качества выпускаемой продукции, снижению процента брака, стандартизации и унификации рабочих мест, сокращению времени на выполнение отдельных технологических операций.
И ещё один стратегический аспект реализации проекта: возможность бесплатного обучения сотрудников, расширения их компетенций. За это отвечают также эксперты ФЦК. И речь идёт не только об одномоментном обучении сотрудников на производственной площадке, но и о воспитании тренеров для последующей передачи полученных знаний. Экспертами также осуществлялась поддержка руководства предприятия в процессе трансформации производственной культуры.
Теперь — и в реальности
Мы так подробно остановились на реалиях программы потому, что результаты всего намеченного уже сегодня можно увидеть в цехах ЭТЗ «ГЭКСАР».
Итак, в качестве пилотного потока был выбран малогабаритный стрелочный универсальный электродвигатель с микропроцессорной системой управления. Как пояснил Рашид Бикташев, «электродвигатель ЭМСУ является лидирующей моделью не только на «ГЭКСАРе», но и в целом на российских железных дорогах, так как он заменил собой все устаревшие модели. Предназначен электродвигатель для эксплуатации на железнодорожном транспорте в составе всех типов стрелочных электроприводов, в том числе для организации высокоскоростного движения поездов типа «Сапсан». По мнению руководителя предприятия, двигатель данной модели без преувеличения можно назвать уникальным за счёт установленной на нём системы управления и возможности работать как на постоянном, так и на переменном напряжении. Число оборотов в минуту можно запрограммировать от 700 до 2600. При этом электродвигатели прежних моделей требовали постоянного обслуживания и отличались такими недостатками, как, например, залипание щёток. На новой модели этих проблем нет и в помине — спокойно работает при температуре минус 60 градусов (неоднократно проверено в камере холода/тепла).
Что же произошло на предприятии за прошедшее время? Суть всего производства — эффективность. Так вот, по оценкам экспертов, за полгода реализации проекта выработка на потоке производства электродвигателей увеличилась на 44%, а кроме того, сокращено время изготовления продукции. В итоге же предприятие может увеличить ежегодный выпуск электродвигателей на 66%, а это на 30 штук в день больше. Общий экономический эффект от всех внедрённых мероприятий составит более 25 млн рублей за год.
Нельзя не упомянуть и «побочный эффект», экономическая составляющая которого впечатляет. Как выяснилось, достижением основных показателей производительности участники проекта не ограничились и «заодно» увеличили скорость упаковки готового изделия на 57%. Последний показатель был достигнут благодаря обустройству эргономичного упаковочного стола, позволяющего рабочему не терять драгоценное время, просто исключив лишние движения и действия.
Существенно сократилось и время покраски электродвигателей. И если раньше приходилось сначала наносить грунтовку, краску, а затем высушивать изделие, переход на порошковую покраску сократил время операции в восемь раз — с 24 до 3 часов. При этом не понадобилось приобретение каких-то дорогостоящих аппаратов — предприятие просто задействовало порошковую камеру окраски, не используемую до этого.
С интересом осмотрели гости и новую котельную, масштабная реконструкция которой была произведена ещё в 2019 году. Вместо старых котлов с низким КПД установили новое оборудование, которое позволяет экономить до 30% газа и существенно сокращает трудозатраты на обслуживание. Серьёзно уменьшились и площади, занимаемые котельной. Как прокомментировал Рашид Бикташев, один старый котёл занимал больше места, чем сегодня вся конструкция.
Но не менее важным результатом преображения старой котельной является для руководителя тот факт, что люди теперь не мёрзнут в цехах, для них удалось создать максимально комфортные условия.
В общем и целом то, что гости в тот день смогли увидеть на «ГЭКСАРе», — результат кропотливой и очень непростой работы целого коллектива людей.
— После вступления в программу на предприятии была создана рабочая группа, которая на протяжении шести месяцев анализировала, генерировала, разрабатывала и внедряла всё то, что мы сейчас с вами увидели, — рассказал, как проходили преобразования на заводе, начальник отдела технического регулирования ООО ЭТЗ «ГЭКСАР» Дмитрий Хорошавин. — Используя инструменты бережливого производства, была создана карта текущего состояния, размеры которой составляли более 10 метров в длину и 2 метра в высоту. На карте отображались все технологические операции и их проблемы, которых мы выявили аж 64. Все они были проанализированы, после чего разработаны мероприятия по их решению.
Дорог каждый сотрудник
В ходе обсуждения итогов реализации проекта неоднократно произносили слово «оптимизация». Заметим сразу: когда речь идёт о заводе «ГЭКСАР», этот термин вовсе не означает увольнения высвобождающихся работников. Наоборот, все они получили возможность обучения смежным профессиям и повышения квалификации. Что ещё раз подтвердил руководитель предприятия.
— Численность сотрудников осталась неизменной, — отметил генеральный директор ООО Электротехнический завод «ГЭКСАР» Рашид Бикташев, — но благодаря сокращению потерь на производстве нам удалось провести перебалансировку высвободившегося персонала на выполнение других операций. Обучение бережливому производству в общей сложности прошли почти 100 сотрудников завода.
Мнение экспертов
А что же говорят об успехе реализации нацпроекта на заводе «ГЭКСАР» эксперты Федерального центра компетенций?
— Темп предприятием взят очень высокий, — комментирует ситуацию руководитель проектов Федерального центра компетенций Юрий Васильев, — и объясню почему. Всех идей, что родились в команде в процессе перемен, было настолько много, что в рамки отведённых национальным проектом шести месяцев они просто не укладывались. Реализация займёт чуть больше времени, но охватит практически все участки данного производства, начиная от изготовления самой маленькой детали в электродвигателе. Меняется абсолютно всё. Но самое главное, мы видим, как изменилось сознание сотрудников. Раньше они даже не замечали потерь при производстве. Сейчас же люди сами готовы предлагать те или иные решения по их устранению. В целом мы видим, по сути, возрождение незаслуженно забытой научной организации труда. Идёт реализация рационализаторских предложений. Сейчас мы уже обучили команду и понимаем, что в последующие три года предприятие достигнет высочайших результатов, намного превысив намеченные показатели.
А вот коллега Юрия Васильева, руководитель проекта Федерального центра компетенций Дмитрий Диденко особо отметил консолидирующую роль в проведении преобразований руководства предприятия:
— Руководство завода было настроено на серьёзную работу, они ждали изменений. Эльмира Бикташева, несмотря на тотальную занятость, нашла время и лично вошла в состав рабочей группы, вместе с нами проводила картирование текущего целевого идеального процесса, прошла весь путь изготовления продукции. Эльмира Эдуардовна была инициатором многих изменений. Этот позитивный настрой передался и коллективу, люди перестали бояться сокращений, и сегодня они хотят двигаться дальше.
А дальше, к слову, будет ещё круче. Ведь в течение всех трёх лет реализации национального проекта работники завода имеют право на бесплатное обучение и участие в команде лидерства. А кроме того, после того, как предприятие успешно защитило поток-образец, добившись отличных результатов, оно может претендовать на получение кредита в размере до 300 млн рублей под 1%. За это уже отвечает Фонд развития промышленности Саратовской области.
Высокую оценку проделанной на заводе работе дал и министр экономического развития Саратовской области Андрей Разборов:
— Участие в нацпроекте — это возможность для предприятий сократить издержки, выйти на новые объёмы производства, повысить качество выпускаемой продукции, а также освоить новые рынки сбыта. «ГЭКСАР» является одним из старейших заводов, и значимо, что именно такое предприятие принимает участие в проекте и получает поддержку по современной методике повышения производительности труда, учитывающей лучший мировой опыт и адаптированной под реалии российского бизнеса. Уверен, что получится растиражировать полученный опыт на все процессы предприятия и вовлечь каждого сотрудника в непрерывное совершенствование своей работы.
К сказанному министром нам остаётся лишь добавить, что останавливаться на достигнутом «ГЭКСАР» действительно не собирается.
— В перспективе за счёт тиражирования полученного опыта мы планируем повысить эффективность сборки блока управления, нанесения порошкового покрытия, а также оптимизировать техобслуживание оборудования и хранения материалов на складах, — поделился планами Рашид Бикташев. — В дальнейшем предприятие планирует оптимизировать такие производственные процессы, как изготовления ротора ЭМСУ, сборки блока управления, порошкового покрытия, хранения материалов на складах, технического обслуживания оборудования. Сегодняшние достижения — это только начало!
Последние новости
- 09:11 Женщина разбилась на мотороллере в Лысогорском районе
- 09:00 Свыше 5 млн россиян планируют построить в ближайшее время дом
08:22 В Саратовскую область на ремонт дворов дополнительно поступят 1 млрд 757 млн рублей- 08:00 В Саратовской области на четыре дня изменяется расписание некоторых электричек
- 06:00 В Саратовской области ожидается слабый дождь
вчера 18:10 На Новой Набережной посадили ивы и декоративные яблони- вчера 18:09 Жительница Федоровского района осуждена за мошенничество в автошколе
- вчера 18:00 Свыше 24 тысячи саратовских школьников приняли участие в олимпиаде по финграмотности
- вчера 17:50 МЧС Саратовской области объявило о желтом уровне опасности
вчера 17:39 В аэропорту "Гагарин" появились новые рейсы из Саратова в Анталию
- загрузить еще